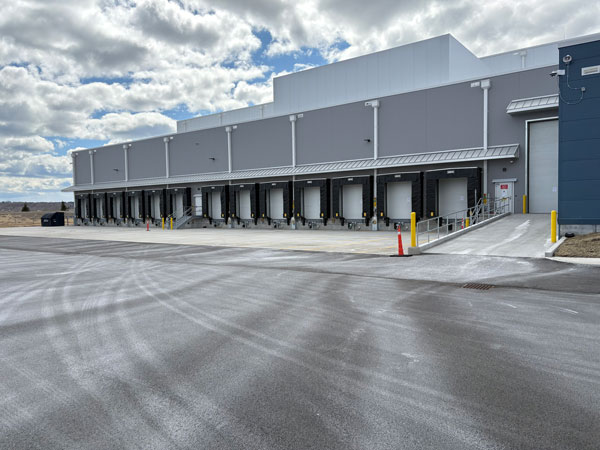
A long-awaited commercial freezer facility has opened along Portland’s waterfront, providing a logistical hub for frozen foods and other products to make their way into and out of Maine.
At 106,000 square feet, the sprawling Maine International Cold Storage Facility is about the size of a typical Home Depot store. With ceilings 50 feet high and seven levels of shelving space, the warehouse will be able handle more than 200 million pounds of frozen product a year. And at minus-10 degrees, the building’s two cavernous freezers are teeth-chattering cold.
The facility opened for business on Feb. 3 with seven customers using the freezer to store frozen haddock, ice cream, lobster bait, and other products. The plan is to slowly ramp up and add two or three businesses per month in the coming year until 20 to 40 companies are using the facility.
The operation is run by Taylor Logistics, a family-owned business based in Cincinnati, Ohio, that operates multiple warehouse facilities in other states. Grant Taylor, vice president of warehouses, said the Portland facility has the capacity to hold up to 21,500 pallet loads of product at a time.
With a turnover of six times a year, the goal is to handle over 100,000 pallets annually, Taylor said, while giving a tour of the facility in late March with Evan Cassidy, the facility’s operations manager. At an average of 2,000 pounds per pallet, that adds up to 200 million pounds or more going through.
“That’s a one- to two-year plan,” Taylor said.
Located on West Commercial Street near the Casco Bay Bridge, the cold-storage building has been more than a decade in the making. The building has offices, a loading area with 13 truck bays, and two massive freezers that take up about 84.,000 square feet. A rooftop solar array will help offset some of the electricity costs.
The facility is expected to provide an economic boost to Portland and Maine by providing a new supply chain option for companies shipping frozen products into or out of Portland.
The freezer will save time and cut transportation costs for businesses that now rely on Boston, New York, and other out-of-state locations for freezer storage for their products. A 2017 study by University of Southern Maine business students estimated that its annual economic impact could be $500-$900 million.
The facility is the first “major piece of cold chain infrastructure constructed in Maine,” said Wade Merritt, president of the Maine International Trade Center.
“Until now, Maine-based businesses that needed reliable cold storage were required to ship products out of state—in some cases as far as the Midwest—due to a lack of local facilities,” he said. “A state-of-the-art facility in Maine will provide significant cost savings for Maine business and position Portland as a global hub for cold chain distribution in this part of New England for exporters and importers.”
While the facility is run by Taylor Logistics, it was developed and is owned by Amber Infrastructure Group and sits on land owned by the Maine Port Authority. In the end, it cost $56 million to build.
The facility, however, provides more than storage for frozen products. It is a transportation hub that is adjacent to the International Marine Terminal where Eimskip USA operates it trans-Atlantic container cargo operations. It’s also just a couple of miles from Maine’s two major highways: interstates 95 and 295.
The facility is also adjacent to a rail spur that connects to CSX’s rail network, and is a short drive from the Portland International Jetport. While there aren’t any products coming into or out of the cold-storage facility by rail or air, those options could provide new opportunities in the future, said Eivind Dueland, senior vice president of Amber Infrastructure.
For now, Dueland said, product is arriving by truck or by sea from the Eimskip container cargo operation next door. He’s pleased with the customer base so far, which includes a mix of national, international, and Maine-based businesses.
He anticipates companies using the freezer facility for products that include seafood, produce, meat, bait products, and animal pharmaceuticals. Based on talks with companies at the Seafood Expo North America in Boston in March, he said it’s clear there’s interest from both importers and exporters.
He doesn’t expect it will take too long for the facility to be operating at or near capacity. “It’ll probably be closer to one year rather than two years,” Dueland said.
For the first couple of months of operation, between one and four trucks were stopping by the facility each day to drop off or pick up product. But when it’s going full bore, it’ll be a beehive of activity.
When operating at capacity, there will be about 40 trucks delivering and picking up product each day. The trucks will range from 18-wheelers down to smaller box trucks, and also include trucks carrying cargo containers from the Eimskip terminal next door.
Inside, employees will run ten modern fork lifts to carry products onto or off the trucks and to and from the huge freezer rooms out back. There, they’ll be stored on floor-to-ceiling shelving that runs seven levels high and has the feel of a huge jungle gym. Four of those fork lifts are known as “turret trucks,” which can operate in very narrow aisles with a mast that can go up dozens of feet to retrieve or place pallets of product.
On this day, the shelves are largely empty, but that will change as more customers come on board in the months ahead and the shelves fill up with a wide assortment of products. Taylor Logistics isn’t saying exactly who its customers are, but there could be a wide variety of food products beyond seafood—whether it be blueberries from eastern Maine or potato products from northern Maine.
“There are a lot of other food products in the state that need to be frozen,” Cassidy said.
For now, the facility is open Monday through Friday. When it gets busier, the company expects to have up to 12 employees working per shift, a number that will grow if it adds a second shift.
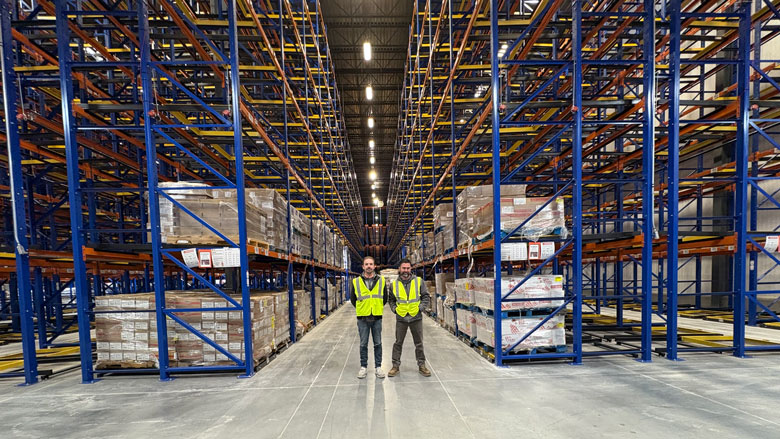